We began our testing with the easy tests first. The Finalized Testing Plan report details our testing procedure for each of these experiments. Our "Cable Actuation" and "Pulley Utlization" tests visually inspected if the device incorporated either of those components. Next was the protrusion and weight test. Here we measured how far the device protruded off the body and we measured the total weight of the device including all of its components. The results from these tests can be seen in the specification sheet located on this page.
For the weight test, we placed the device onto a scale from Dr. Lerner's lab. The completely assembled device was placed on the scale in order to get an accurate reading of the total weight. This included the battery, motor, harness system, etc. The total weight measured from this scale was 2.6 kg or 5.73 lbs.
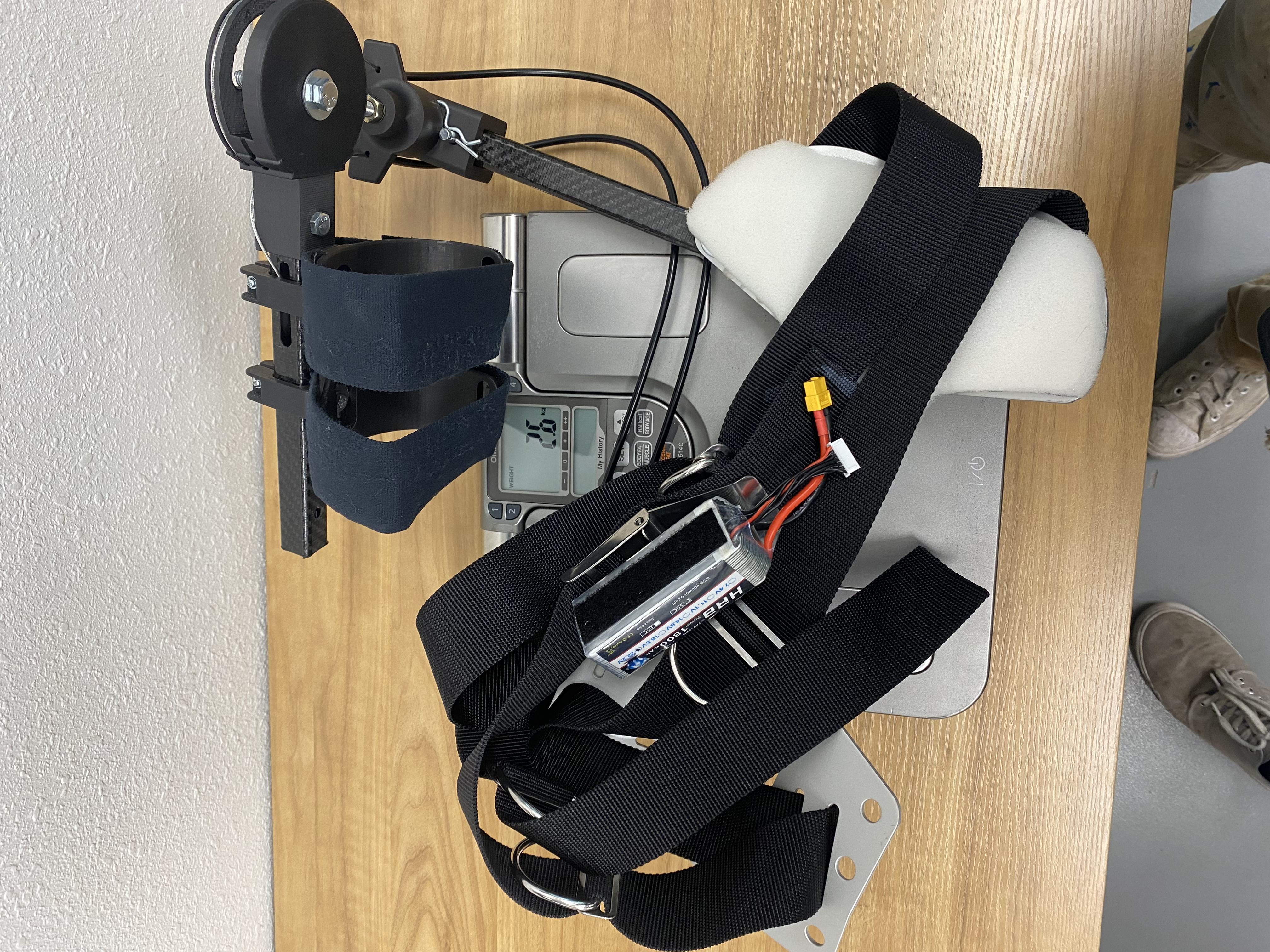
For the protrusion test, we used a tape measurer to determine the maximum protrusion of the device. We measured at all points that were visually the highest extrusion. For our device, this was the pulley, motor, and block. Our design requirement was to remain under 10 cm (3.94 in.) of protrusion from the body. In the images below, the measured value was about 4.5in for the block and just over 4in for the motor. The pulley extruded less than both these values. Unfortunately, these protrusions do exceed the design requirement, however this is still acceptable by the client as seen in the spec sheet.
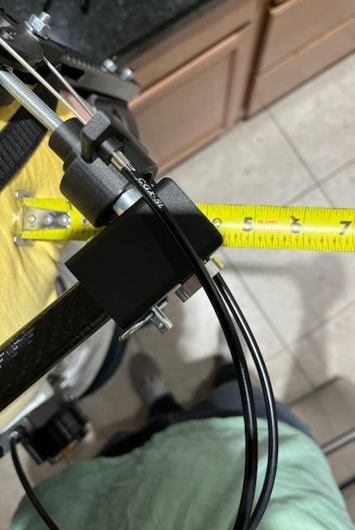
Block Protrusion
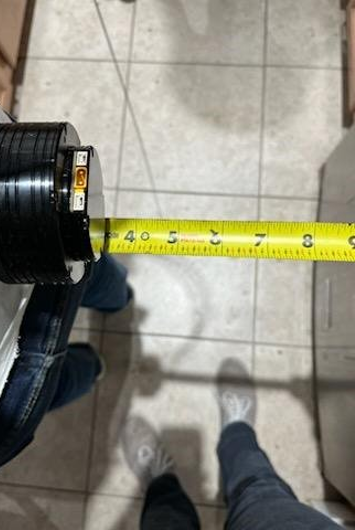
Motor Protrusion
The piece that broke in the above video was the shaft found on the block that interfaced the pulley with the rear bar. This shaft was designed as one component connected with the block and was printed out of PLA only. PLA is far from strong enough to handle the load sent through it during the test so Dylan machined an aluminum shaft inside the NAU machine shop to replace this component. The rest of the block was reprinted with Onyx inlaid with carbon fiber to add extra strength to its component.
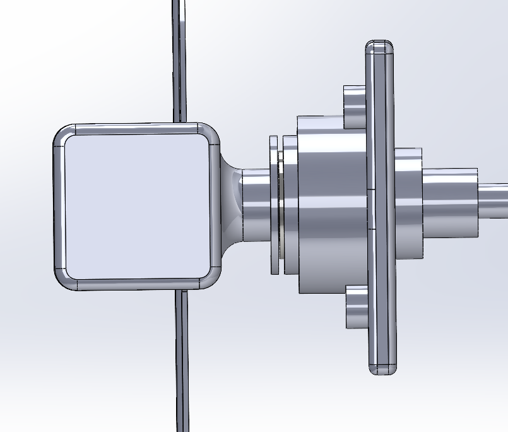
Original Shaft Design - PLA
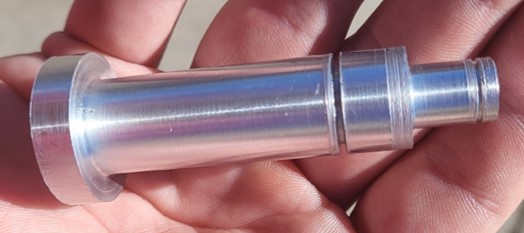
Revised Aluminum Design
We expected that our device would be able to increase the timed ability of a user to hold a weight in front of them. From our endurance test, we found that each test subject experienced an increase in time to hold a weight while assisted versus unassisted. The team is ecstatic to have gotten these kinds of result. Future testing will be done to refine these numbers by conducting more trials, but due to the nature of this submission those results cannot be present now. The testing results and final spec sheet are pictured below.
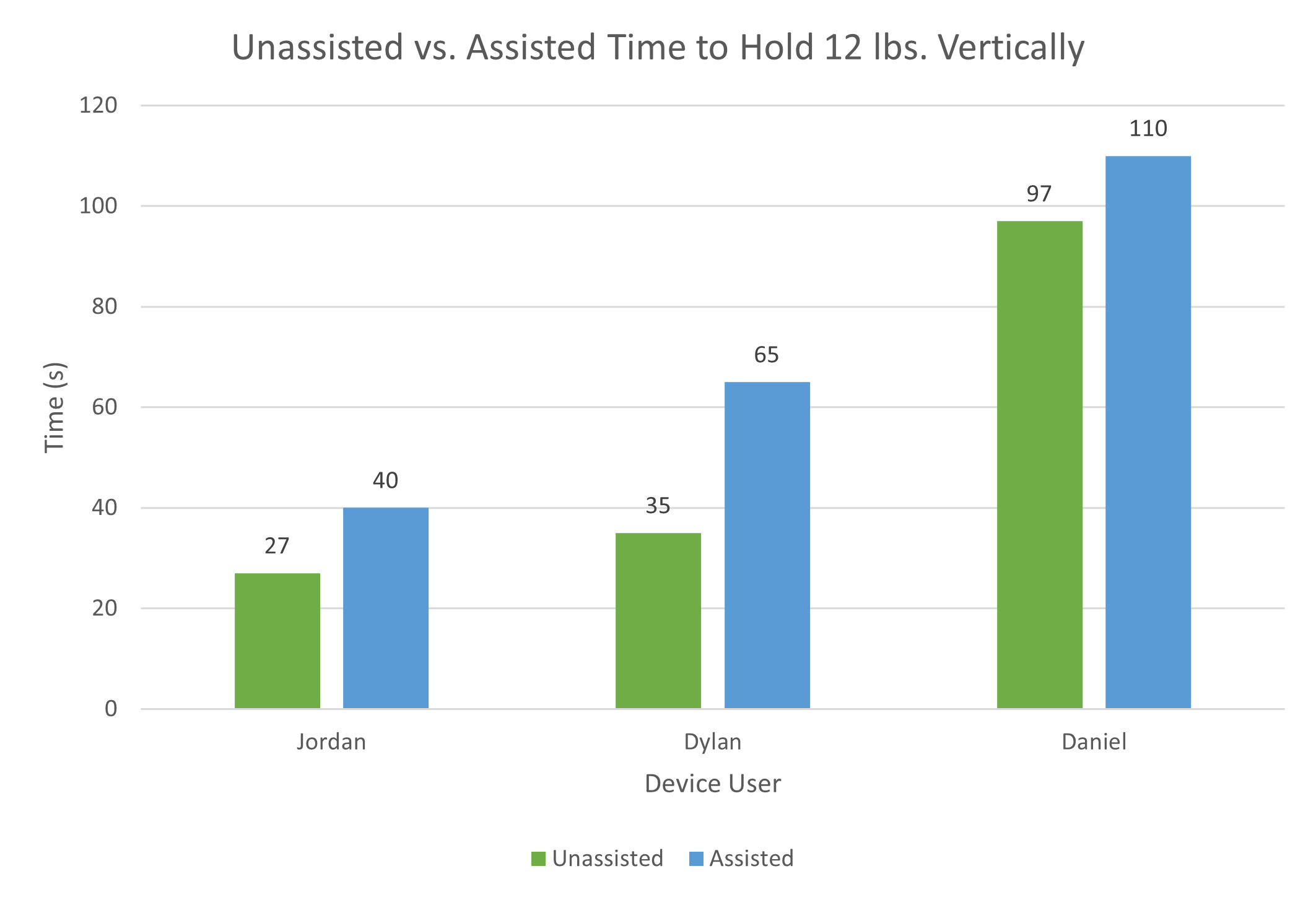