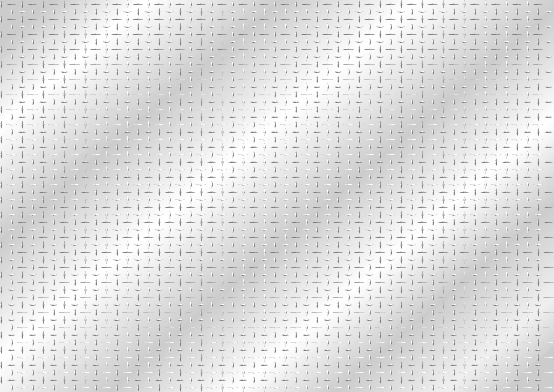
The purpose of this project was to design, fabricate, and load
test a 1:10 scale model for a replacement steel bridge. The scale model bridge
has a minimum clear span of 18 feet, and will be tested with a randomly placed
load of 2500 pounds. Requirements for the bridge as well as scoring criteria
were provided by AISC. The scoring of the bridge is based upon deflection,
construction time, and weight.
A unique solution using cold-formed, high-strength steel was
implemented to minimize the deflection and weight of the bridge. The design
was completed using the SAP2000, RISA-3D, and COSMOSWorks software packages.
Results from the models were compared to provide independent verification of
member forces and deflections. Hand calculations were based upon the AISC
Manual of Steel Construction and the AISI Cold-Formed Steel Design Manual.
Fabrication of the bridge was performed in the NAU CEFNS
Fabrication and Manufacturing Shop by the team members and volunteers. Load
testing was performed at the annual 2009 Pacific Southwest Regional Conference
hosted by the University of Hawaii, Manoa.
This project could not have been either completed or successful
with out the help and support of many people, companies, and organizations.
For this reason our deepest gratitude goes out to the following:
•
Northern Arizona University College of Engineering
Forestry & Natural Sciences.
• Dr. Wilbert Odem, Dr. Joshua Hewes
• CEFNS Manufacturing Shop
• Schuff Steel Company
• Mr. Jay Allen
• Gecko Steel Truss
• Mr. Dennis Smarra
• TOR Engineering
• Mr. Bob Hubbard and Mr. Dave Merrell
• Praxair Welding Supply
• Mr. K. Bryan Noyes
• Prescott Steel and Welding Supply
• Copper State Nut and Bolt Co.
• Danny Harris and Eli Reisner
•
Lastly, we would like to thank the NAU Student Chapter of ASCE and all of our friends and family who supported our efforts.
This year the ASCE Pacific Southwest Regional Student Conference
was hosted by the University of Hawaii at Manoa. This is a three day event where 18
universities compete in several events.
The team
captains are very proud of the results
from this years conference.
This is the
first time in the past several years that
NAU has entered a qualifying bridge.
Although the bridge did not place very
well in the construction speed category,
the team participated extremely well in
the categories of lightness and stiffness
with 3rd and 4th place, respectively.
Overall the NAU Steel Bridge Team took 7th place out of 18 schools in
competition. As a school, NAU took 7th place overall in the PSWRC
2009 Conference.


















Exaggerated SAP2000 Lateral-Torsional Frame Buckling
The analysis of the bridge was performed primarily in a
simplified RISA-3D model. 79 unique
load combinations were applied to the model to determine a full force envelope
for all members. P-δ effects were
considered in this model. The force data was output to Microsoft Excel, and
summary tables were created for the design of individual members.
A
more complex finite element model in SAP2000 was created modeling partial
fixities of the end moment
connections,
partial fixities of the bracing frame, the proprietary top chord, and the
custom tapered
columns. This SAP2000 model was used for verification of the
RISA-3D model through member
force
matching and for determining the buckling modes. 150 load cases were applied
to this
model,
using modified stiffnesses from the stressed state of the equivalent static
load case
in
the buckling load cases to account for P-δ effects on the buckling of the
structure.
COSMOSWorks
was used in conjunction with the SAP2000 model to determine the partial
fixities
of the required moment-resisting connections to increase the accuracy of the
model.
The design of the bridge began by investigating a simple beam
bridge and 3 different basic truss types: a Pratt truss, a Warren truss, and a
bowstring truss. During preliminary analysis, the simple beam and bowstring
truss were eliminated for either excessive deflections or fabrication and
construction complexity. Through multiple iterations, a combination Pratt and
Warren truss was selected to minimize the number of members and connections as
well as the inherent stiffness provided.
Each individual member and connection was designed for the
maximum compression and tension expected. LRFD design methodology was used,
with a 1.2 load factor applied to the 2500 pound loading to be conducted at
competition. An additional accidental
eccentricity was applied to compression forces in members to ensure that small
variations during fabrication did not cause failure at competition.
20 gage, 45 ksi yield galvanized steel was selected for all tube
members while 20 gage, 55 ksi yield galvanized steel was used for the top
chord. 14 gage, 36 ksi steel was selected for the connections and columns.